Por EloInsights, com colaboração de Thiago Leite
- Segundo e último artigo da série introdutória sobre indústria 4.0 aprofunda em desafios da transformação digital dentro do setor industrial.
- Granularidade de dados de maquinário e integração vertical de sistemas aparecem como pontos a serem trabalhados pelas organizações.
- Aculturamento de pessoal, aumento de capacidade analítica e incorporação de competências digitais também são desafios.
No primeiro artigo desta série introdutória à indústria 4.0 no contexto do mercado brasileiro, destacamos alguns dos conceitos fundamentais dessa nova forma de olhar para os desafios da indústria; uma abordagem que se baseia na integração de diferentes tecnologias habilitadoras a desafios típicos das operações para gerar impactos positivos no negócio.
Entre essas tecnologias estão inteligência artificial, advanced analytics, internet das coisas e robotização. Falamos sobre como essas competências habilitadoras precisam ser utilizadas como lentes, que permitirão a cada organização encontrar formas de entregar impacto dentro de suas especificidades.
Neste segundo artigo, abordaremos desafios que são característicos da transformação digital na indústria:
- A necessidade de integração de sistemas em diferentes níveis das organizações, desde o plano dos processos da produção física até o do planejamento de negócio;
- A capacitação e a mudança de perfil do tipo de trabalho realizado, com a urgência da integração de maior capacidade analítica.
A integração entre IT e OT no ambiente industrial
“Uma diferença importante da transformação digital da indústria é que se trabalha com informações mais granulares, que precisam ser monitoradas constantemente”, diz Thiago Leite, gerente sênior da EloGroup. “Saímos da IT (Tecnologia da Informação) pura, no nível 4 – de Business Planning, segurança, servidores e workstations, e-mails, databases e aplicações – e vamos para dimensões de TA (Tecnologia de Automação) e OT (Tecnologia Operacional), nos níveis mais inferiores.”
Ele se refere ao modelo ISA95, da International Society of Automation, que propõe uma forma de organizar esses diferentes tipos de sistemas em cinco níveis:
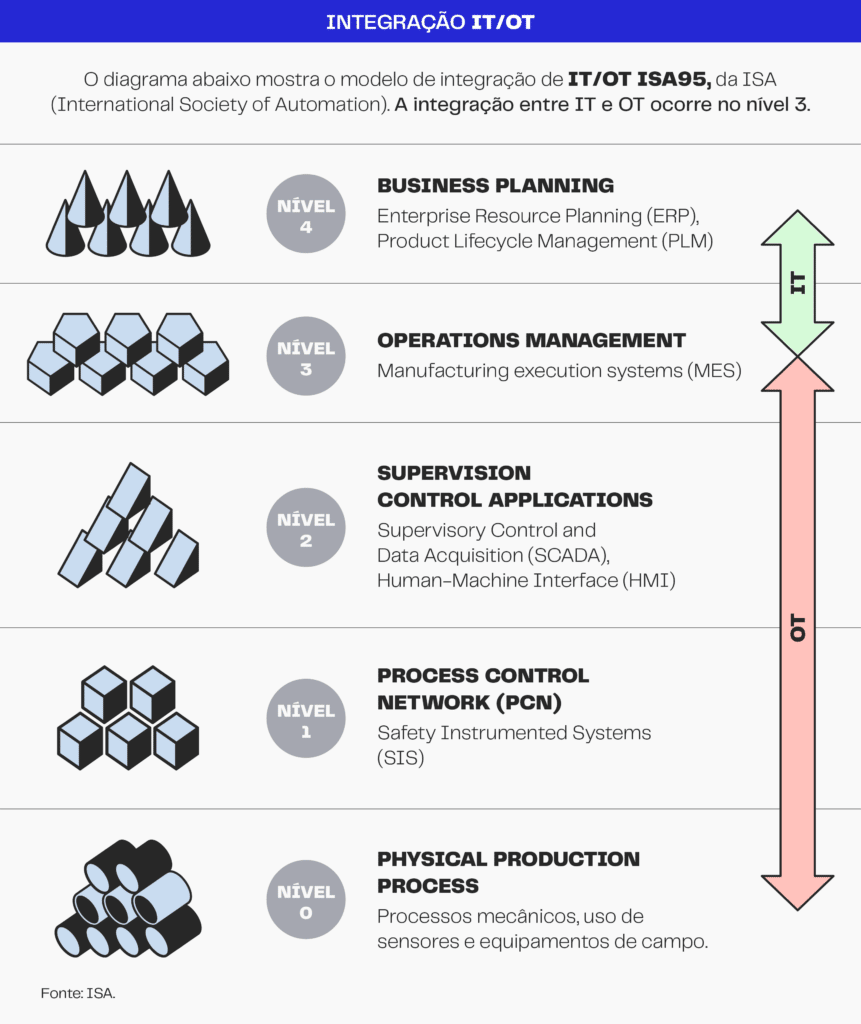
No plano da produção física, que envolve processos mecânicos e equipamentos de campo, a informação produzida tem essa característica granular e muitas vezes desestruturada, o que torna seu processamento um desafio mais complexo. A gestão da manutenção do maquinário de uma planta industrial, por exemplo, depende de informações como temperatura e níveis de vibração no funcionamento do equipamento. Nesse cenário, a otimização de processos e ganho de eficiência passa a depender do uso desses dados e da integração deles com outros sistemas.
Ainda que outros setores da economia também lidem com esse problema da granularidade de dados, na indústria destaca-se a criticidade dos mesmos, no sentido da garantia da segurança operacional das fábricas, estabilidade do processo produtivo e proteção do meio-ambiente. Esse ponto é chave pois a ausência de monitoramento de dados na granularidade necessária pode resultar em acidentes ou até desastres ambientais.
Um exemplo das especificidades do uso de dados na indústria: para consolidar a chamada “overall equipment efficiency” (OEE), indicador de quão próximo de seu potencial máximo de produção um equipamento trabalha, é necessário cruzar dados de diferentes fontes e processos para compreender se o equipamento analisado está indisponível por causa de um defeito em si próprio ou em outro equipamento, se a performance de produção está compatível e se a qualidade do produto na ponta está dentro das especificações. Tradicionalmente, em função da ausência de dados granulares disponíveis e integrados, o cálculo é feito de forma manual. Para agilizar e tornar essas operações mais precisas, a aplicação de automação e inteligência artificial é uma possibilidade.
Nesse olhar vertical, a transformação digital da indústria deve gradualmente penetrar os diferentes níveis, desde os mais básicos na esfera regulatória, da automação tradicional, como gestão de alarmes e de malhas industriais, até os mais complexos, que envolvem modelos avançados de otimização do planejamento de produção, da configuração operacional das plantas, controle avançado de processos e gestão da saúde dos ativos.
“A substituição do trabalho mais manual, com a medição automática desses indicadores e a integração de sistemas, viabiliza uma tomada de decisão mais autônoma no chão de fábrica”, afirma Leite. Tais mudanças não impactam apenas em requisitos do maquinário, mas pedem especialmente uma adaptação cultural e técnica das pessoas.
Capacitação e construção de bases na indústria 4.0
A crescente necessidade de conhecimento sobre novas tecnologias em todos os níveis da organização naturalmente impacta na urgência por investimento em inteligência digital.
Um dos desafios na indústria é garantir que os colaboradores tenham acesso a dados que permitirão uma tomada de decisão menos subjetiva, dentro de uma cultura orientada à experimentação.
Em muitos casos, no entanto, as plantas industriais ainda não têm maturidade tecnológica para gerar maior sinergia entre as áreas de gestão e produção. É fundamental investir em bases, elementos organizacionais e técnicos que vão possibilitar o uso de tecnologias mais avançadas de forma perene, e não apenas pontualmente. Isso se traduz em construir infraestrutura, padronizar processos e aculturar as pessoas.
Em termos de ações práticas, um exemplo simples é garantir conexão a redes de dados em áreas fundamentais da planta industrial, permitindo o rápido fluxo de informações relativas à operação e à produção, e viabilizando o uso das mesmas em sistemas que podem trazer os já citados ganhos operacionais, na forma de maior agilidade e previsibilidade de custos. Outro exemplo é a atualização e aumento da capacidade de servidores no sentido de viabilizar o processamento de maiores volumes de dados locais das fábricas e transferi-los para nuvens corporativas, onde podem ser enriquecidos com outros dados pertinentes como custos e receitas industriais.
Outros tipos de investimentos “fundacionais”: aplicar inteligência de dados diretamente na linha de produção, com execuções preditivas que vão diminuir perdas e evitar manutenções custosas; integrar sistemas, habilitando o acesso, de forma estruturada e estratégica, a dados de fornecedores que viabilizem previsões em tempo real e tragam maior eficiência na logística e na cadeia produtiva como um todo. Vale pontuar que, ainda que muitos fornecedores industriais ofereçam acesso às tecnologias habilitadoras e às vezes até centros de competências com acesso direto aos dados fabris para trazer insights às fábricas, o protagonismo pela jornada e a responsabilidade por internalizar capabilities continua sendo das indústrias.
Nesse contexto, a capacitação da força de trabalho deve levar em conta o impacto causado nas pessoas pela adoção dessas tecnologias. O primeiro ponto está na valorização e no acolhimento de quem passa por essa transição.
“No nível mais operacional, é realmente urgente a capacitação das pessoas em um sentido de ressignificar o conceito de trabalho na indústria”, diz Leite. Há uma crescente demanda pela aplicação de conhecimentos relacionados a estatística, na interpretação de resultados e números. As atividades perdem o caráter braçal e demandam rapidez na leitura de alertas e na adoção de procedimentos padrões.
Programas de aculturamento e capacitação em áreas-chave, como advanced analytics, devem ser incluídos no escopo das organizações. É importante que essa capacidade analítica venha de dentro da própria indústria, de forma que todo o conhecimento setorial possa ser aproveitado com uma nova dimensão de análise.
É fundamental obter, em nível organizacional, um profundo conhecimento das tecnologias habilitadoras e da relação entre as áreas de IT, AT e OT. Das principais limitações, até aspectos de arquitetura e integração. Para isso, há dois principais caminhos: cultivar parceiros muito próximos que ajudem a formar essas capabilities, ou internalizar a criação de competências.
No primeiro caso, um exemplo de capacitação “inorgânica” seria a aquisição de uma startup que domine a tecnologia habilitadora em questão, como sensoriamento, advanced analytics, entre outras. A incorporação de um time já capacitado à organização tende a se reverter em resultados mais rápidos.
No segundo caminho, a capacitação orgânica pode levar mais tempo, mas há também algumas medidas que podem ser aplicadas e ajudar a trazer resultados, como a implementação (caso a necessidade for por análise de dados avançada) de um Centro de Excelência em Analytics (CoE Analytics), cuja função é alinhar a visão de advanced analytics à estratégia de negócio da empresa, aprimorar capabilities em diversas áreas organizacionais, aumentar a qualidade dos dados com padronização e aplicação de boas práticas para análises mais avançadas, e contribuir na atração e retenção de talentos de alto nível técnico.
Como já discutimos, não existe uma tecnologia ou solução únicas que possam ser aplicadas universalmente aos diferentes segmentos da indústria. Cada setor tem processos e um conjunto de casos de uso específicos. Isso se explica, em parte, pela variação dos ativos: na indústria automotiva, grandes prensas e os robôs de funilaria desempenham um papel central nas linhas de produção, enquanto na siderurgia quem ocupa essa posição é o forno. Já na de celulose, é a máquina de papel e o turbogerador.
Portanto, cada uma dessas indústrias terá que encontrar seus próprios caminhos, dentro de suas realidades específicas, e lidar com os diferentes desafios que emergem dessa pluralidade de cenários, que incluem ainda os variados estágios de amadurecimento digital de cada organização, entre outros aspectos tratados anteriormente. Mas, independentemente de onde cada empresa se encontrar nessa trajetória não-linear, os fundamentos detalhados até aqui garantem um guia para que elas possam se mover no sentido de se apropriar das tecnologias habilitadoras como lentes capazes de destravar os potenciais da indústria 4.0 em cada cenário.
THIAGO LEITE é gerente sênior da EloGroup.