By EloInsights
- Low-code technologies, which require little to no programming, have matured in recent years, allowing their application to the discipline of process management.
- From this intersection, process automation appears. Automating the use of technologies enables process management to be done in a systematic, robust, and rapid manner.
- The automation method developed by EloGroup allows an organization to move from a desire for digital transformation to a fully functional, approved, and in-production system in 30 days.
In recent decades, systems that accelerate software development by delivering “pre-programmed” elements have grown in popularity, and this trend has even earned a name: the low-code or no-code movement, referring to the reduced dependence on coding knowledge to develop certain programs. Previously, you had to write the code for a particular form from scratch, but now platforms include a form generator. The same applies to databases, which today already connect front-end with back-end in a much simpler and more secure way, ensuring high performance.
It is from the intersection of this “low code” world with the discipline of process management that process automation is born, explains Leonardo Haag, senior manager at EloGroup.
“It is a technology and a mindset that helps you understand the logic of that business problem and format a solution”, explains Haag. “Process automation comes from a world where low-code technologies have matured. These platforms appeared to take the discipline of process management and transform it into a system. They offer resources so that this discipline can be done systematically”.
It is not enough to create a form – you also need to analyze the process that the form is involved in. “This is the backdrop of automation”, Haag explains. “It is a technology that supports process management”.
Another crucial point is that the maturation of these technologies allows for speed and consistency gains in implementations. Furthermore, there is a large community of developers working on that product to improve its performance and usability.
“Technologies that used to only do workflow turned into BPMS [Business Process Management Suite]; then IBPMS, encompassing intelligent processes; and later DPA [digital process automation]. In other words, these technologies came to bring more repertoire and to solve more business problems”, says the manager.
The EloGroup Process Automation Method
Haag points out that, within EloGroup, the process automation method that ensured the successful implementation of dozens of projects appeared in 2017 and has since been refined and improved based on continuous learning from its use in different contexts.
The use of a “time box” system – which sets a well-defined time limit for each project – was important for the success of the method. “Working with a time box was fundamental; initially, we thought doing it in parallel would be better, but it wasn’t. The old method was good but not scalable enough. So, we went through a learning process to define this new method”.
He explains, step-by-step, how this method works in practice, from the client’s desire to automate a process to the delivery of a completely functional first version, ready for production.
Initiation, Needs Identification, and Technical Framing
It all starts with an organization’s desire for digital transformation. In this case, the client recognizes an automation opportunity. This starts a preliminary work of designing a possible solution that responds to this first desire. Business needs are mapped, possible system integrations, form fields; in short, the functional scope expected from that project.
At this stage, the analysis goes deep enough for the project to be framed in one of the “time box” lanes: projects that last two, three, four weeks, and others of extremely high complexity that can be framed in a time box of up to two months. This ensures visibility into the size of this process; a large draft is formed there.
Since the project itself has not yet started, several of these initiations can be carried out in parallel. “This way, I create an agile culture”, says Haag. “We need full client involvement. A type of pact is made. We agree on days when we will need them in the schedule. It is a great preparation, where we inform how the work will be done, define who will be involved, etc. We explain what is to come”.
In this first stage, the process is studied from various aspects – for example, what is its proposal? What is its volume? What is the size of the demand for it? How many people are involved in its stages? These are some of the variables that affect the design of the automation.
In a second moment, immersion is carried out with the aim of raising the requirements of that process: which activities will be automated, form behaviors, specific rules. Technical framing is done, leading to the decision on the best solution for it. This solution is defined and then approved by the client, who gives formal confirmation for the next stage, which is the development of a prototype.
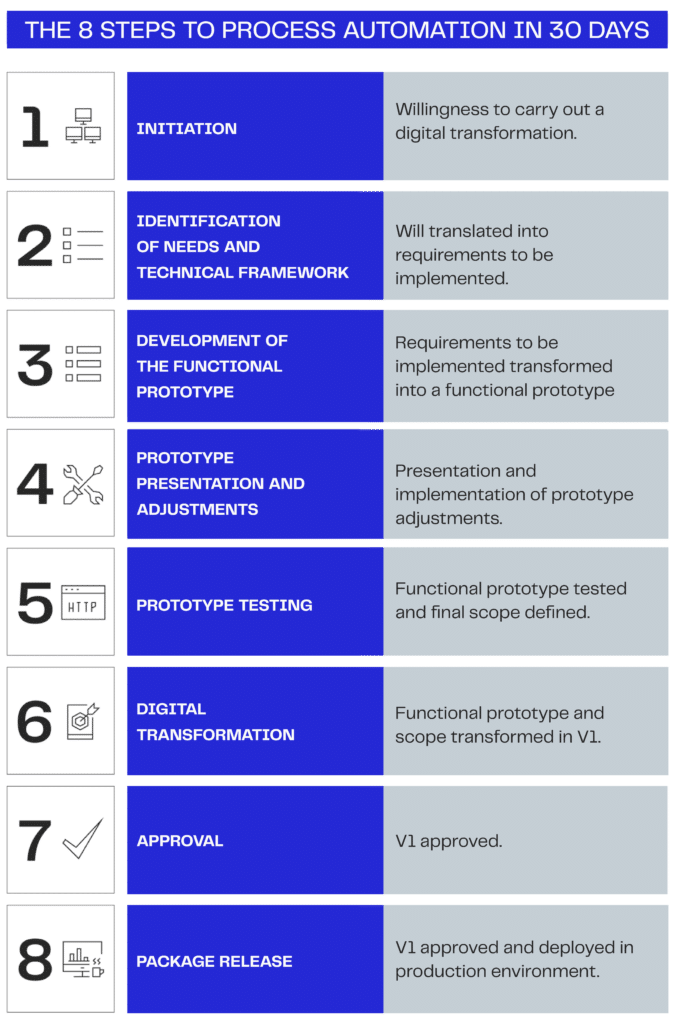
Prototype Development, Testing, and Adjustments
After initiation and technical framing, with all information gathered about the process, a solution defined and approved by the client, the team continues to produce a functional system prototype.
This prototype needs to be functional because, at this stage, the organization conducts tests with real data, getting closer to the final experience. This stage is crucial as it generates a list of necessary adjustments.
“The functional prototype is the most realistic you can get within the established time”, explains Haag. “Its use generates a list of realistic, precise adjustments because it promotes experience with real data. In the case of exceptions, it allows you to see how they behave”.
At this stage, it is important for all actors involved in the process to be integrated into the tests so that the process can mature, and the list of necessary corrections is complete.
Prototype is Transformed into v1, Approved, and Put into Production
After having the list of adjustments and implementing them, a “v1” – the first version of the automated system – is built. Following this, in the project’s final stretch, the approval phase begins. “It works like a war room”, Haag says. “We only leave after approval. At this stage, new functions or requirements are no longer discussed. For projects with a 30-day time box, the approval phase lasts two days. This is when the commitment is completed”.
After the system is approved, it finally moves to the production stage. This is also the time to create the technical documentation that gathers all the implemented business rules and conduct load tests if necessary to ensure stability even in high-demand scenarios.
Finally, the service is put into a production environment. “This way, we can move from an automation desire to a first approved version deployed in a production environment”, concludes Haag. “It is ready to be used”.